Photographs from Fylde Guitars continue to flood into my inbox. When the guitar arrives here, I'll probably write the whole thing up into an article - I find the whole subject of acoustic guitar construction fascinating and I hope a few other iTalk Guitar members will, too!
In any case, our latest batch of pics starts pretty much where the last lot left off; we'd got to the stage where the slots for the guitar's inlays around the soundhole had been cut - and here they are being filled in.
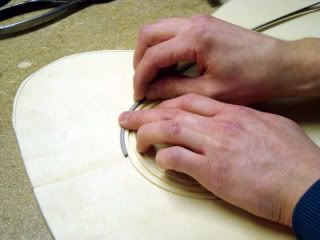
The bracing on the underside of a guitar's soundboard is there for two principle reasons: firstly to add strength and secondly to influence the way in which the top vibrates as this has a great effect on the sound of the guitar. Each maker has his own formula for bracing - here we see the classic X brace (pioneered by the Martin guitar company) surrounded by Roger Bucknall's own tried and tested formula for producing a solid, rich tone from the soundboard.
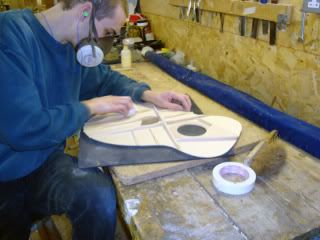
The back of the guitar receives some bracing, too. Two centre reinforcing strips along the 'seam' or joint in the bookmatching, plus horizontal braces to add strength.
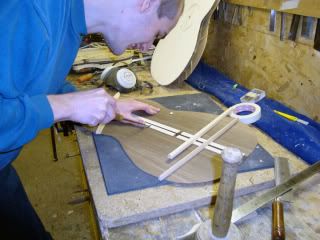
Now it's time to begin putting the various elements we've seen constructed together. Here, bracing is being added to the guitar's sides - once again, this is for strength, in order to make the 'box section' of the guitar sturdy enough to withstand the various slings and arrows that we musicians inflict on our treasured instruments!
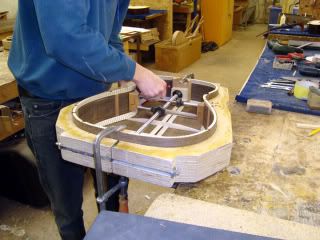
Once the various components of the guitar's soundbox are ready for final assembly, the top and back are both test fitted to the sides to ensure a good fit. Here, the back is being scrutinised before gluing:
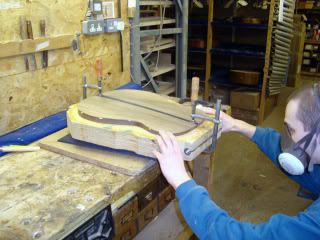
The final stage before the body is finally glued together - test fitting the top:
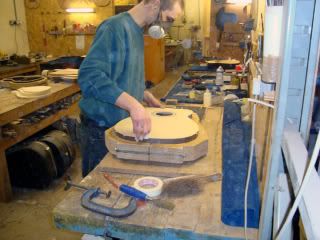
I'm hugely indebted to Roger Bucknall at Fylde Guitars for sending me these pictures. As many musicians know, it's possible to form a very special bond with an instrument and these images will ensure that I will literally know this acoustic guitar inside and out!